Fertigungslinie für Lithiumzellen: Ein umfassender Überblick
Eine Fertigungslinie für Lithiumzellen ist ein hochspezialisiertes Produktionssystem zur Montage von Lithium-Ionen-Batterien, die für eine Vielzahl von Anwendungen wie Elektrofahrzeuge (EVs), Unterhaltungselektronik, Speicherung erneuerbarer Energien und mehr unerlässlich sind. Diese Produktionslinien sind für die Ausweitung der Batterieherstellung von entscheidender Bedeutung und gewährleisten Konsistenz, Leistung und Qualitätskontrolle bei jeder produzierten Zelle.
Lithium-Ionen-Batterien werden aufgrund ihrer hohen Energiedichte, ihres langen Lebenszyklus und ihres relativ geringen Gewichts bevorzugt, was sie ideal für tragbare Elektronikgeräte und Elektrofahrzeuge macht. Da die Nachfrage nach diesen Batterien steigt, insbesondere mit dem Wachstum des Marktes für Elektrofahrzeuge, wird der Bedarf an effizienten, automatisierten Fertigungslinien immer wichtiger.
---
Wichtige Schritte im Herstellungsprozess von Lithiumzellen
1. Elektrodenvorbereitung
- Mischen der Aufschlämmung: Der Prozess beginnt mit dem Mischen von aktiven Materialien (wie Lithiumkobaltoxid oder Lithiumeisenphosphat), Bindemitteln und Lösungsmitteln, um eine Aufschlämmung zu erzeugen.
- Beschichtung: Die Aufschlämmung wird auf Metallfolien aufgetragen (typischerweise Aluminium für die Kathode und Kupfer für die Anode). Dieser Schritt ist entscheidend, um eine gleichmäßige Verteilung des aktiven Materials sicherzustellen.
- Trocknen: Nach der Beschichtung werden die Elektroden in einem Ofen getrocknet, um die Lösungsmittel zu entfernen und sicherzustellen, dass die Beschichtung fest ist und gut auf den Metallfolien haftet.
- Kalandrieren: Die getrockneten Elektroden werden durch eine Kalandermaschine geleitet, um sie auf eine bestimmte Dicke zu verdichten und ihre Dichte zu verbessern.
2. Elektrodenschneiden
- Die Elektroden werden auf präzise Größen zugeschnitten und sind bereit für den Einbau in die Batteriezelle. Dazu gehört das Zuschneiden sowohl der Kathoden- als auch der Anodenmaterialien, damit sie in das Zellendesign passen.
3. Zellmontage
- Stapeln oder Wickeln: In diesem Schritt werden Anode, Kathode und Separator zusammengebaut. Die gebräuchlichste Konfiguration ist die „Jelly Roll“-Methode (für zylindrische Zellen), bei der Anode, Kathode und Separator spiralförmig aufgerollt werden. Bei Pouch-Zellen sind die Elektroden schichtweise gestapelt.
- Laschenschweißen: Die Elektroden werden mit Laschen verbunden, die zur Herstellung der elektrischen Verbindungen verwendet werden, sobald die Zelle vollständig zusammengebaut ist.
4. Elektrolytfüllung
- Nach dem Zusammenbau werden die Zellen mit einer Elektrolytlösung gefüllt. Der Elektrolyt ist wichtig, um die Bewegung der Ionen zwischen Anode und Kathode während des Ladens und Entladens zu erleichtern.
5. Zellversiegelung
- Nach dem Einfüllen des Elektrolyten wird die Zelle in einem Gehäuse versiegelt, das typischerweise aus Metall oder Kunststoff besteht. Der Versiegelungsprozess muss sicherstellen, dass die Zelle luftdicht und vor äußeren Umwelteinflüssen geschützt ist.
6. Entstehungsprozess
- Anfängliches Laden/Entladen: Die Zelle durchläuft einen ersten Lade- und Entladezyklus, der als Formationsprozess bezeichnet wird. Dieser Schritt aktiviert die Chemie der Zelle und stellt sicher, dass die Batterie ordnungsgemäß funktioniert.
- Alterung: Die Zelle wird für einen bestimmten Zeitraum unter kontrollierten Bedingungen gelagert, um den Elektrolyten zu stabilisieren und eine Stabilisierung der Batterieleistung zu ermöglichen.
7. Prüfung und Qualitätskontrolle
– Die Zelle wird einer Reihe von Tests unterzogen, um sicherzustellen, dass sie den erforderlichen Spezifikationen entspricht. Diese Tests können Folgendes umfassen:
- Kapazitätstest: Sicherstellen, dass die Zelle die Nennleistung liefert.
- Lebensdauertest: Beurteilung der Lebensdauer der Batterie.
- Sicherheitstests: Sicherstellen, dass die Zelle Überladung, Kurzschlüssen und anderen potenziell gefährlichen Bedingungen standhält.
8. Verpackung und Endkontrolle
- Sobald die Zelle alle Tests bestanden hat, wird sie gemäß den Kundenspezifikationen verpackt und etikettiert. Bei der Endkontrolle wird auf äußere Schäden geprüft und sichergestellt, dass die Batterie voll funktionsfähig ist.
---
Schlüsselkomponenten eines Herstellung von Lithium-Ionen-Pouchzellen
1. Elektrodenbeschichtungslinie
- Beschichtungsmaschinen: Diese Maschinen sind dafür verantwortlich, die Aufschlämmung gleichmäßig auf die Metallfolien aufzutragen.
- Trockenöfen: Trockenöfen entfernen das Lösungsmittel und verfestigen die Beschichtung.
- Kalandermaschinen: Komprimieren Sie die beschichteten Elektroden auf die gewünschte Dicke.
2. Elektrodenschneide- und Montagelinie
- Elektrodenschneidemaschinen: Sorgen für präzises Zuschneiden der Elektroden auf die erforderlichen Größen.
- Laschenschweißmaschinen: Diese Maschinen schweißen die Laschen an die Elektroden, um den elektrischen Kontakt sicherzustellen.
3. Zellmontageausrüstung
- Wickel- und Stapelmaschinen: Je nach Zelltyp (zylindrisch oder Beutel) werden diese Geräte verwendet, um die Elektroden in die endgültige Konfiguration zu bringen.
- Elektrolyt-Füllgerät: Injiziert den Elektrolyten kontrolliert in die Zelle.
- Versiegelungsmaschinen: Versiegelt das Zellgehäuse und sorgt so dafür, dass es luftdicht und stabil ist.
4. Formations- und Testgeräte
- Formationsausrüstung: Führt den ersten Lade- und Entladezyklus durch, um die Zelle zu aktivieren.
- Batterietestausrüstung: Testet die Leistung der Batterie, einschließlich Ladekapazität, Innenwiderstand und Zyklenlebensdauer.
- Alterungskammern: Lagert Zellen unter kontrollierter Temperatur und Luftfeuchtigkeit, um Stabilität zu gewährleisten.
---
Vorteile einer vollständig integrierten Fertigungslinie für Lithiumzellen
1. Hohe Effizienz
- Die Automatisierung in jedem Schritt des Herstellungsprozesses ermöglicht schnellere Produktionszeiten und geringere Arbeitskosten. Die Automatisierung sorgt außerdem für Konsistenz, reduziert menschliche Fehler und steigert die Gesamteffizienz.
2. Skalierbarkeit
– Moderne Fertigungslinien können je nach Bedarf vergrößert oder verkleinert werden. Neuere Maschinen und Geräte ermöglichen eine Massenproduktion ohne Qualitätseinbußen.
3. Präzision und Qualitätskontrolle
- Die Präzision moderner Geräte stellt sicher, dass jeder Aspekt der Zelle, von der Elektrodenbeschichtung bis zur Versiegelung, mit hoher Genauigkeit ausgeführt wird. Strenge Prüfprozesse tragen zur Gewährleistung der Produktqualität und -sicherheit bei.
4. Kosteneffizienz
- Bei der Produktion in großem Maßstab sinken die Kosten pro Einheit erheblich, wodurch die Produktion von Lithium-Ionen-Batterien kostengünstiger wird. Ein effizienter Materialeinsatz und die Reduzierung von Abfällen tragen ebenfalls zur Senkung der Produktionskosten bei.
5. Flexibilität
– Moderne Produktionslinien für Lithiumzellen können Batterien unterschiedlicher Größe und Chemie aufnehmen und bieten Herstellern die Flexibilität, auf verschiedene Marktanforderungen einzugehen.
---
Herausforderungen bei der Herstellung von Lithiumzellen
1. Materiallieferkette
- Die Herstellung von Lithium-Ionen-Batterien basiert auf bestimmten Rohstoffen wie Lithium, Kobalt, Nickel und Graphit. Die Verfügbarkeit und Preisschwankungen dieser Materialien können sich auf den Herstellungsprozess auswirken.
2. Hohe Anfangsinvestition
- Der Aufbau einer Produktionslinie für Lithiumzellen erfordert erhebliche Vorabinvestitionen in Ausrüstung und Anlagen. Dies gilt insbesondere für Produktionslinien mit hohem Durchsatz, die fortschrittliche Automatisierung und Präzisionsmaschinen erfordern.
3. Umweltbedenken
- Bei der Herstellung von Lithium-Ionen-Batterien kann Abfall entstehen, und die Entsorgung dieser Batterien, insbesondere am Ende ihres Lebenszyklus, stellt Umweltprobleme dar. Hersteller müssen sicherstellen, dass sie über nachhaltige Praktiken verfügen, einschließlich Recycling und Minimierung gefährlicher Nebenprodukte.
4. Batteriesicherheit
- Mit zunehmender Größe und Energiedichte von Batterien (insbesondere in Elektrofahrzeugen) wird die Gewährleistung der Sicherheit der Zellen während der Herstellung und des Betriebs noch wichtiger. Jeder Herstellungsfehler, wie z. B. Verunreinigungen oder falsche Abdichtung, kann zu Sicherheitsproblemen wie thermischem Durchgehen, Bränden oder Explosionen führen.
---
Schlussfolgerung
Eine Fertigungslinie für Lithiumzellen ist ein hochentwickeltes System zur effizienten und sicheren Herstellung hochwertiger Lithium-Ionen-Batterien. Es integriert fortschrittliche Maschinen und Automatisierung, um jeden Schritt des Produktionsprozesses zu bewältigen, von der Elektrodenvorbereitung bis zur Endprüfung. Angesichts der wachsenden Nachfrage nach Lithium-Ionen-Batterien in Bereichen wie Elektrofahrzeugen und Speicherung erneuerbarer Energien ist der Aufbau einer zuverlässigen und skalierbaren Produktionslinie von entscheidender Bedeutung, um sowohl Marktanforderungen als auch Sicherheitsstandards zu erfüllen. Da sich die Technologie ständig weiterentwickelt, werden Verbesserungen in den Produktionslinien es der Industrie ermöglichen, die steigende Nachfrage nach leistungsstarken, kostengünstigen Batterien zu decken.
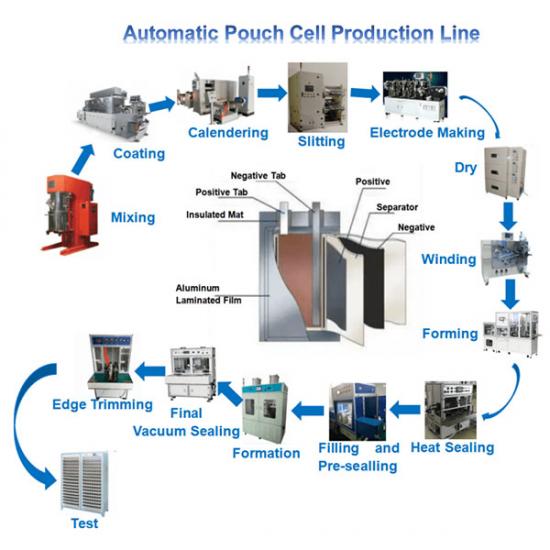